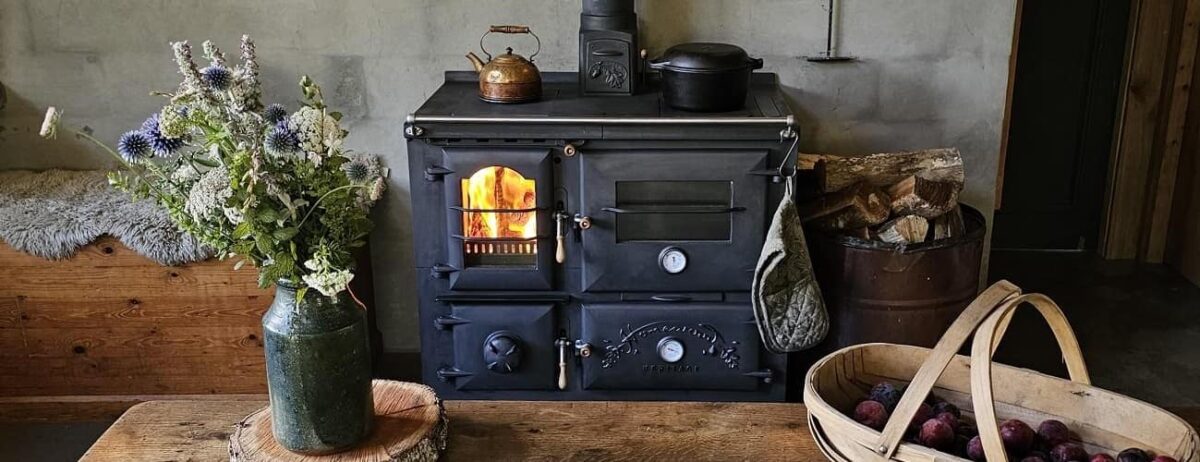
A Labour of Love
It is my pleasure to announce the successful completion of an ambitious, multi-year project redeveloping our Homewood Heritage stove, enhancing all units we build from now (2025) into the future. It may look awfully like the same reliable Heritage that people have been loving for over two decades (and that’s because it is still the same quality stove, design uncompromised during the upgrade!) – in this article we’ll look at what has been refined.
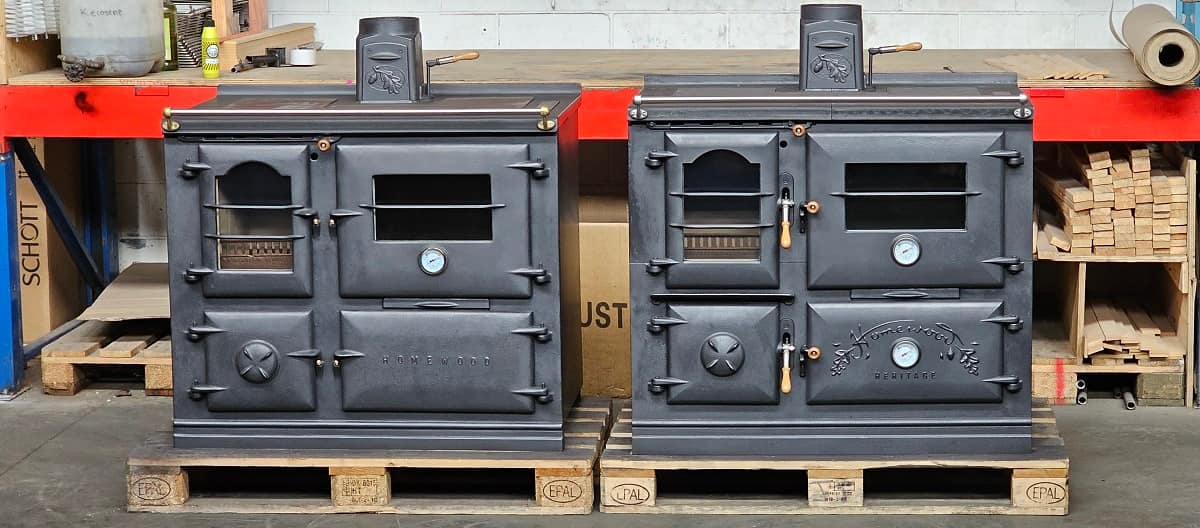
(Original on left, updated on right: if viewing on your phone, this article is best read turned sideways!)
So yes, despite looking very similar (again: by design!), this picture represents thousands of hours of work. Every single iron piece you can see as part of the stove to the right (plus a whole bunch more internal you can’t see) has been manufactured from completely new production-grade foundry patterns, patterns that we have built from scratch inhouse.
Why redevelop? My father’s original handmade (and largely-wooden) foundry patterns (that he first worked on in the 1990s!) were starting to show their age, requiring increasingly-frequent maintenance to keep in good working order. Transforming all of the tooling involved over to high-quality, production-grade foundry patterns was always going to be an ambitious undertaking for a small company like ours, but it has been a necessary investment to secure our future and also presented us with an exciting opportunity. Fully rebuilding from the ground up at the foundational pattern level like this meant we could bring across improvements from later models, and address any and all little niggles we’ve ever had, improving things at the foundry, for our production processes and for the end user.
For the uninitiated, in order to make something from cast-iron, each foundry pattern requires two boxes per unique part, forming the front and rear halves of the article:
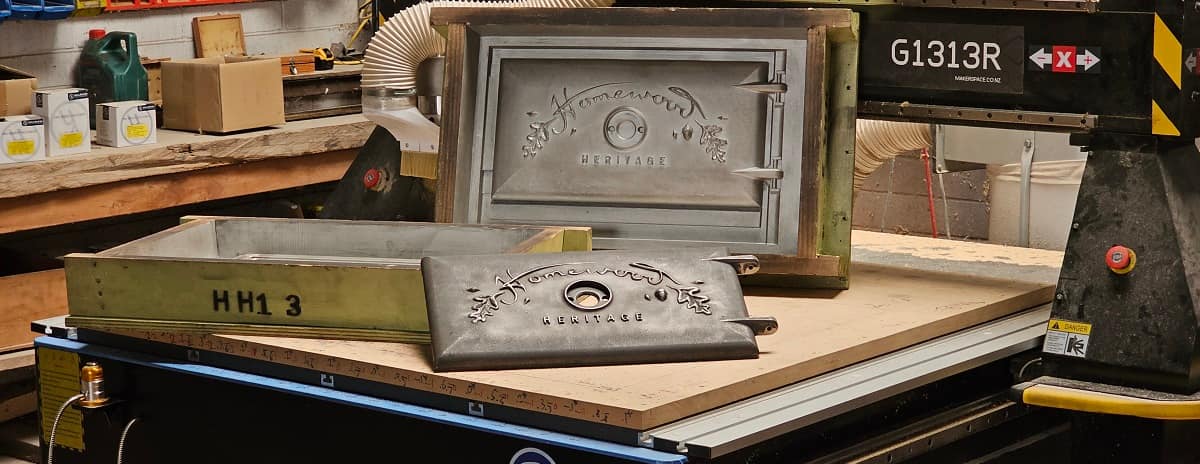
(The patterns for the redesigned lower oven door, with the resulting iron article leaning in front)
At the foundry, sand gets compacted into each of these boxes to form sand molds, these molds are removed and pressed together, leaving the pattern ready to be filled again with sand and restart the process (hence why casting is a powerful manufacturing tool, dating back thousands of years). Pushed together like this a void is created in the middle of the sand mold in the shape of the desired article, and into this void the molten metal is poured, allowed to solidify and eventually broken out.
We have gone through and rebuilt every one of these patterns (first virtually as 3D models, allowing us to check out different ideas and confirm compatibilities; sometimes even 3D-printing a physical representation of the final part, to triple check fit tolerances) and we have incorporated every possible improvement as we did so – some obvious but most less-obvious, including many so subtle that they’re only ever going to be appreciated by us here at the factory.
We are thrilled with the result.
For the end user, it’s the more obvious ones that are going to be most impactful, so let’s take a look at those!
Enhancements
We have added a thermometer to the lower oven door, and what was fairly flat “HOMEWOOD” foundry lettering on this door has now been upgraded to some of Dad’s rather lovely hand-carved detailing:
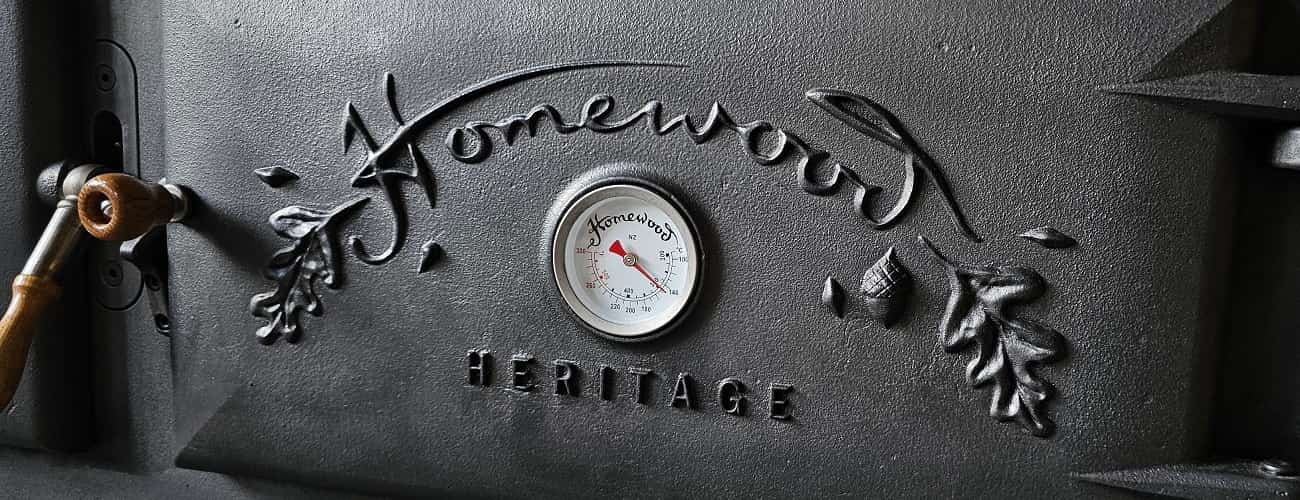
Previously – despite best efforts to clearly communicate otherwise in our Operating Manuals – some customers would seldom (or even never!) use the lower oven on their Heritage, suffering under the misconception that it was merely a warming compartment. Not so – it is a wonderful oven in it’s own right: running cooler than the main oven and producing the most tender, melt-in-your-mouth slow roasts. Initially we were somewhat hesitant about adding this second thermometer, fearing it might detract from the ‘clean’ and understated look of the stove, or stray too far from the original design, but instead it looks like it was always meant to be there, and I know all future customers are going to appreciate the clear temperature reading and use the lower oven more as a result.
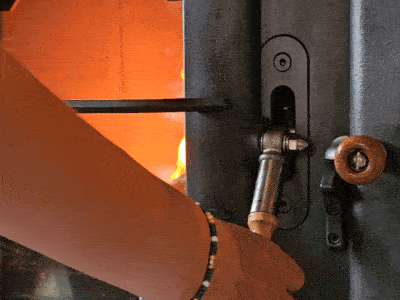
The firebox and ash doors (combustion side) now have the same easy-to-use and positive-sealing hook-style handles first seen on our Companion model, and further refined here.
This represents something we have been wanting to do for (not even joking here) fifteen years, but had been out of our reach because the pattern change to the doors and front panel castings required to make this style handle work would then set off other needed pattern changes that would cascade through too many parts to be viable: changes only now possible and all achieved thanks to this complete overhaul.
Entirely new on both oven-side doors is a gravity latch mechanism.
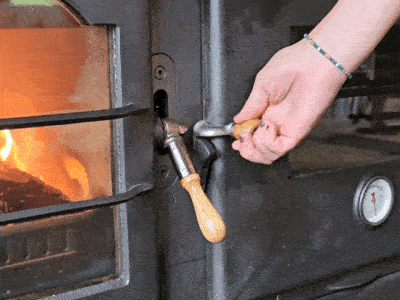
Still able to just be pushed shut, it’s now more positive and much longer wearing than the previous system.
Less glamorous, but certainly still impactful – we’ve chopped the larger castings up, introducing control-joint style expansion gaps. See if you can spot the subtle lines in earlier photos!
These too were something we were a touch nervous might compromise the purity of our aesthetic, but already feel like have always meant to be there. These joints function to help relieve any stress and tension in the metal from the endless cycles of expansion and contraction that comes with the heating and cooling of the fire. Having the previously giant castings now being half their size makes things much more manageable on the foundry and production floors too, which sure doesn’t hurt.
The stainless steel shield (and rack shelf) in the top oven, there to mitigate fireside heat bias, has been relocated to the outside of the left wall oven panel, leaving an all-iron oven interior, for easier oiling and seasoning:
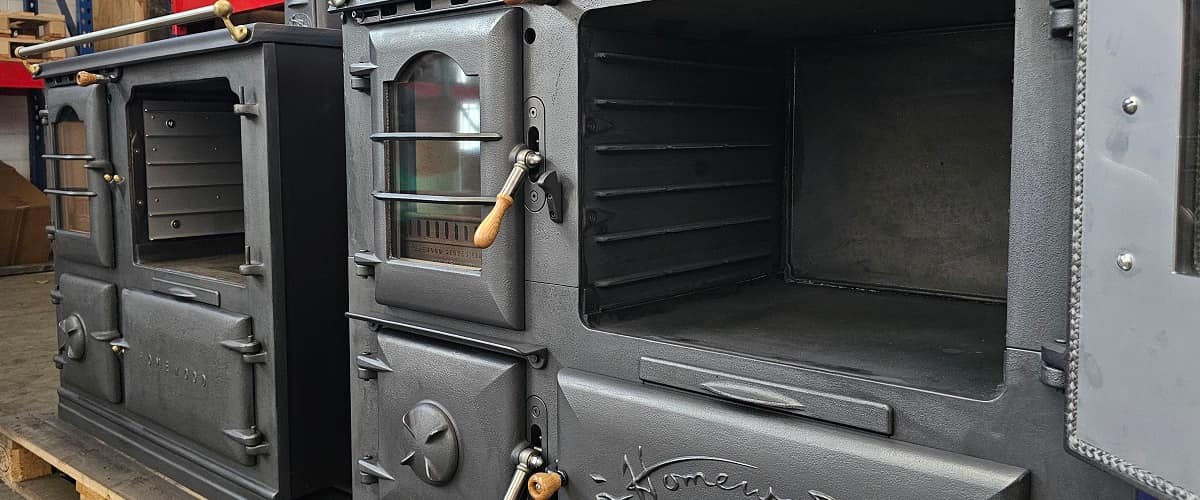
(Original in background, updated on right)
We’ve added a completely new piece you can spot here too, between the ash compartment and firebox doors: a little ash shelf, to catch any little spills of ash released when opening the door above.
The ash compartment is tidier in construction and more compact, allowing extra insulation all around, and a more snug fit for the ashpan:
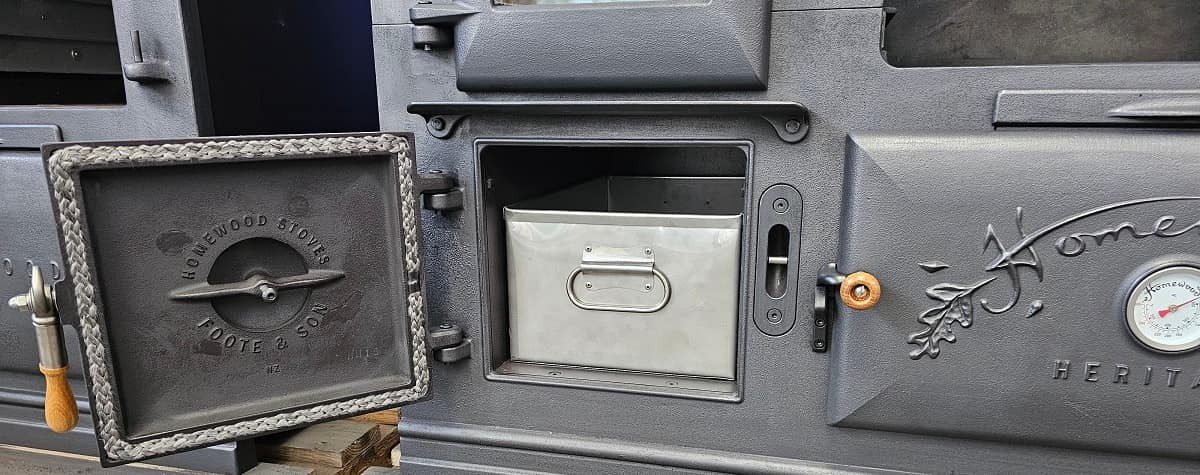
Spot here also the first time “HOMEWOOD STOVES” has appeared in iron, and a little maker’s mark added to the inside of the ash compartment door. The firebox itself is also neater (though dimensionally unchanged), with bricks and water jackets made easier to install or replace.
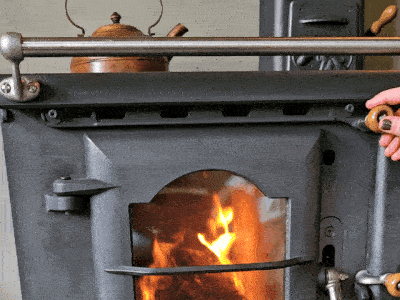
The top air control now has nice little cast iron stops, which likely seems a fairly inconsequential change, but previously with the slider closing only on its posts we’d occasionally have people inadvertently bend these pins (prompting a revision to the Operating Manual, and a caution about gentle use!). Bent pins then make the air slider stiffer and harder to operate, which means more force is employed and starts a vicious circle of more bending until replacement – eek! In recent years we had mitigated this significantly by employing a nice shoulder bolt and washer/spring system, but nice to have now side-stepped this completely (but please don’t try to jam your slider, this not a challenge, ha!).
In similar vein, we’ve redesigned the double-glazed window glass sandwich. Expansion and contraction in the firebox can see the securing screws move and work loose over time, and customers have had to take care to not overtighten else risk cracking the high-heat specialty glass. Again: not challenging you to try, but it should now basically be impossible for the end user to overtighten these screws.
One final and more major change that you may have spotted from the very first side-by-side photo: we have increased the overall height, from what was 870 mm tall previously, floor to stovetop, now 900 mm: standard kitchen bench/counter height not just here in New Zealand, but also Australia, UK and much of the world (sorry USA: did briefly consider 3 feet/915 mm, but the metric system beat you out here! Can always raise by 15 mm – or more – by installing on a small plinth to match surrounding counter tops if so desired!). This extra 30 mm has let us insulate the underside of the stove even further.
Everything else, all other dimensions including the firebox and circulation channels, how it runs and circulates, the grade of cast iron and quality of non-iron components, have all faithfully remained the same (or thickened/strengthened!), without compromise.
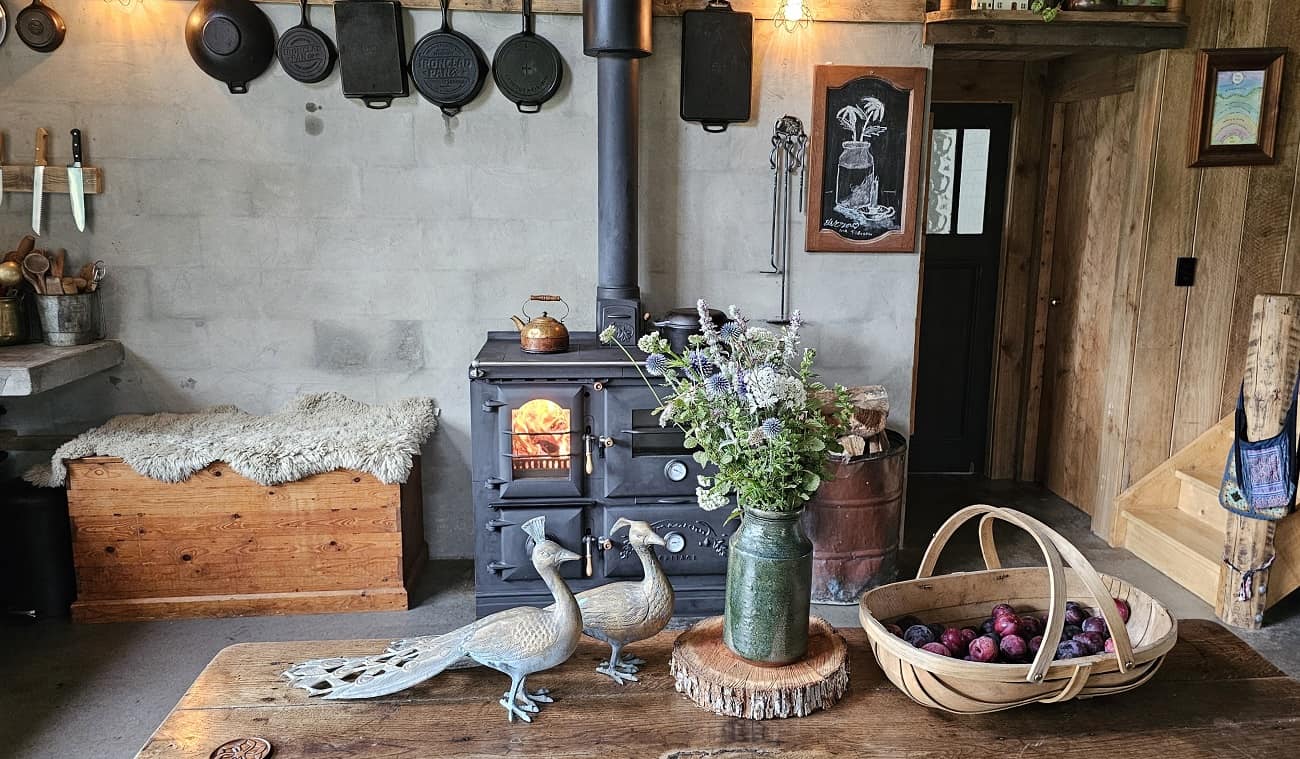
The result is an already-fantastic stove being even better – truly best-in-class, second only to our very own, peerless, Homewood Matriarch model.
Aaaaaaaaaaaaaaaaaaaaaaaaaaaaaaaaaaaaaaaand, on the subject of the Homewood Matriarch (which has many parts in common with the Homewood Heritage as starting point) I am very happy to announce that we have also put this absolutely impressive unit through the same full repatterning project: we are building the very first of these improved Matriarch stoves right now, and much of 2025 will be spent busy on their production!
Over the upcoming weeks, expect to see this website get updated with lots of nice new Heritage and Matriarch photos (and videos!), tweaked and adjusted Installation Specifications and Operating Manuals.
Acknowledgements
This has been a very large undertaking for our small business, and I would like to acknowledge a key few people.
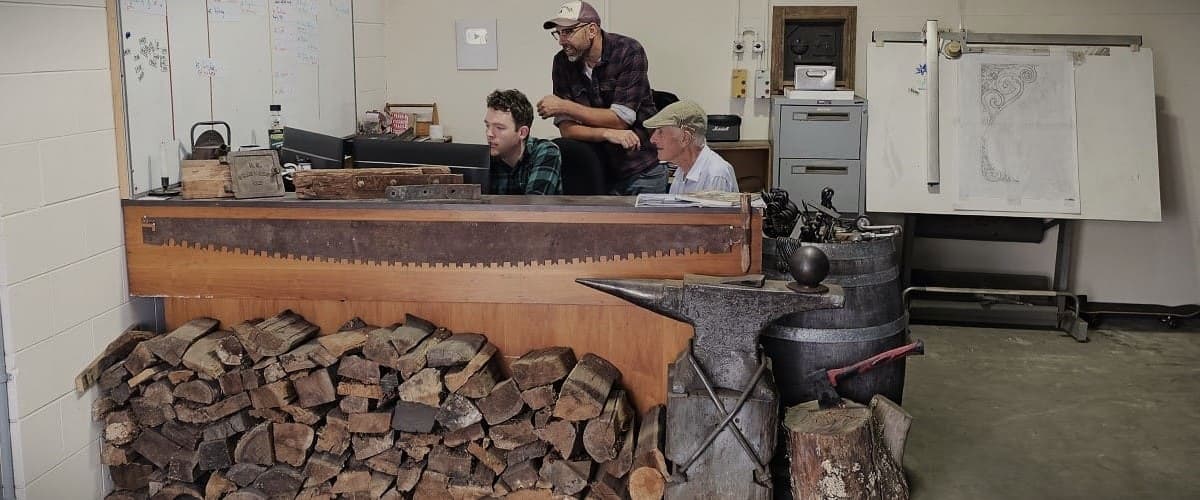
(Andrew, Zak [that’s me!] and David)
My father, David, for both his original design and his creative input during this redevelopment process. And for trusting me with his baby! Having him call in to the factory from time-to-time and make suggestions of what seem like very minor tweaks and subtle improvements is a big part of how we have managed the end result to remain so faithful to his original vision.
On reading this article, Dad wanted to say something of his own:
It is very pleasing to see these developments. Well done Zak for your design input and for making it all happen. And well done Andrew for all the modeling work and your rapid progress learning the art of pattern making.
I felt from the very beginning of production at Homewood that the injection of an extra degree of precision was going to be needed to get production happening in a more fluid and proper way, but that I was not the one capable of providing that element. I love creating things, but I only ever really enjoy making one of anything!
It is very gratifying to see Homewood forging forward into the future beyond where I could take it, in very capable hands.
Andrew, our Product Development Engineer, who has outdone himself with all the CAD design, prototyping, engineering work and patternmaking involved in bringing this all to life (and an extra special personal thanks-and-sorry from me to Andrew for putting him through more mid-project additions and changes than is likely good for anyone’s sanity!). Well done.
It’s actually really lovely: Andrew first worked for us as a teenager, and returned to us late in 2022 to work on this project as his first job once graduated as Master of Engineering Design. Please don’t poach him from me just yet, but he’s excellent at what he does and I’m sure will go far.

(Andrew with the pattern for the lower oven door on the Homewood Matriarch)
Carl, master stove builder, our longest serving fulltime employee. He has assembled more stoves than anyone, and had many good points of input on pattern adjustments for improving the production process.
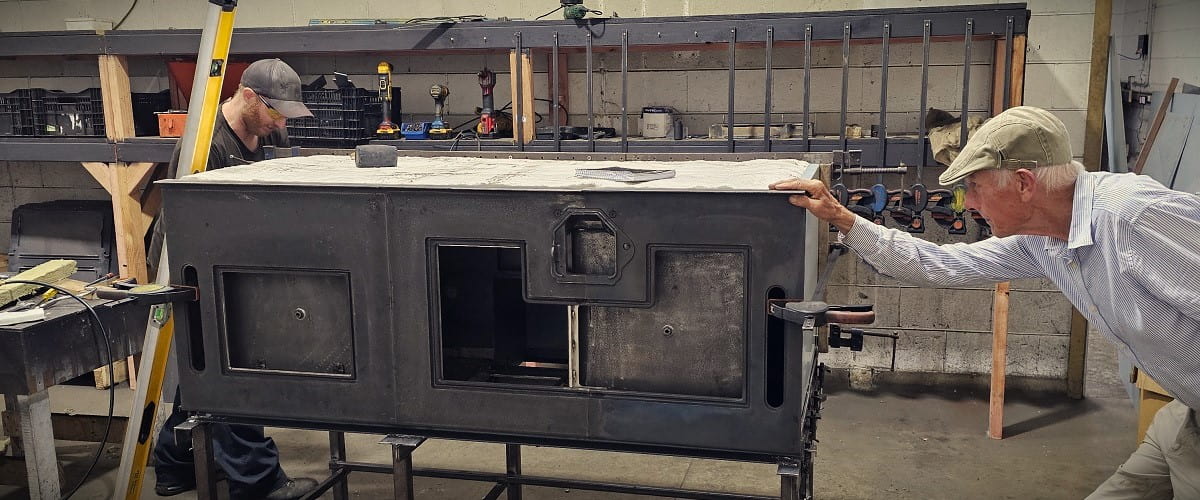
(David, right, checks out the top that Carl, left, and I have just added to the first of these new Matriarch stoves)
Luke, our Operations Manager and my 2IC, who has risen admirably to the task of keeping regular production ticking along so smoothly during this extended project and transition period, taking lead on adapting and improving our processes across the board.
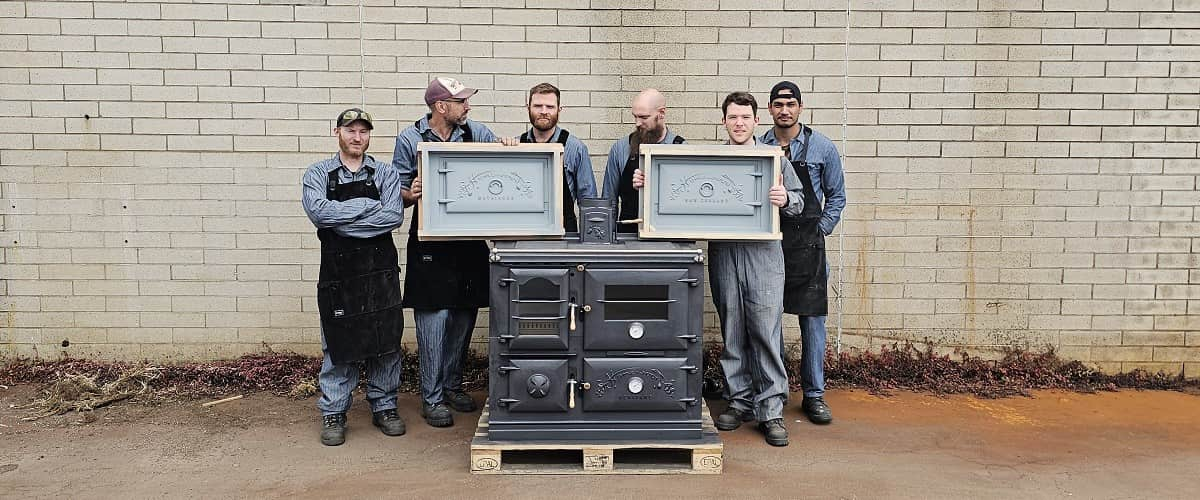
(Carl, Me, Luke, Simeon, Andrew and Chris – Steve taking the photo and Shane absent)
Here’s to a great 2025 and beyond with a great team!
All our suppliers old and new, but most notably Murray, previously of Cast Components foundry, Palmerston North, for his advice and output over many years, and for his help (and long-suffering!) in keeping the old patterns alive; and more recently John and the rest of his team at Technicast foundry, Wanganui, for all their suggestions, trials and willingness to experiment on the new patterns and parts: to brilliant result.
Olly, of Osborne Restoration in the UK, for his generosity in response when I threw ideas at him from the other side of the world, and for his abundant sharing of photos, expertise and experience with all the wonderful old ranges he restores (check out his Instagram!) that sparked many thoughts.
All those customers who have given us valuable feedback on their experiences with their Homewood over the years, one of whom in particular I will single out and thank (but you’re all great!): Luc, for his very strong opinion that the lower oven really ought to have a thermometer too. It stuck with me, and that ended up becoming one of the last major very-near-end-of-project additions, and I’m glad it was!
And finally every single customer these last 20+ years, whether you’ve ever shared photos or feedback with me or not, that have allowed this business of ours to survive and thrive in the face of many challenges (a certain disruptive pandemic saw this project, among others, be delayed multiple times). Any of you existing customers who may be reading this, worrying that you’ve been obsoleted: rest assured you have the same high quality stove we’ve built our reputation on, that spare parts remain available, and we will always preserve the original patterns.
One sad (but-not-too-sad!) side effect of this project: production on the Homewood Companion is on pause for 2025 (at least!), while we focus on the production of these new-and-improved Heritage and Matriarch stoves, and evaluate if we are prepared to put the Companion through this same process. You can read more about this here.
– Zak, January 2025